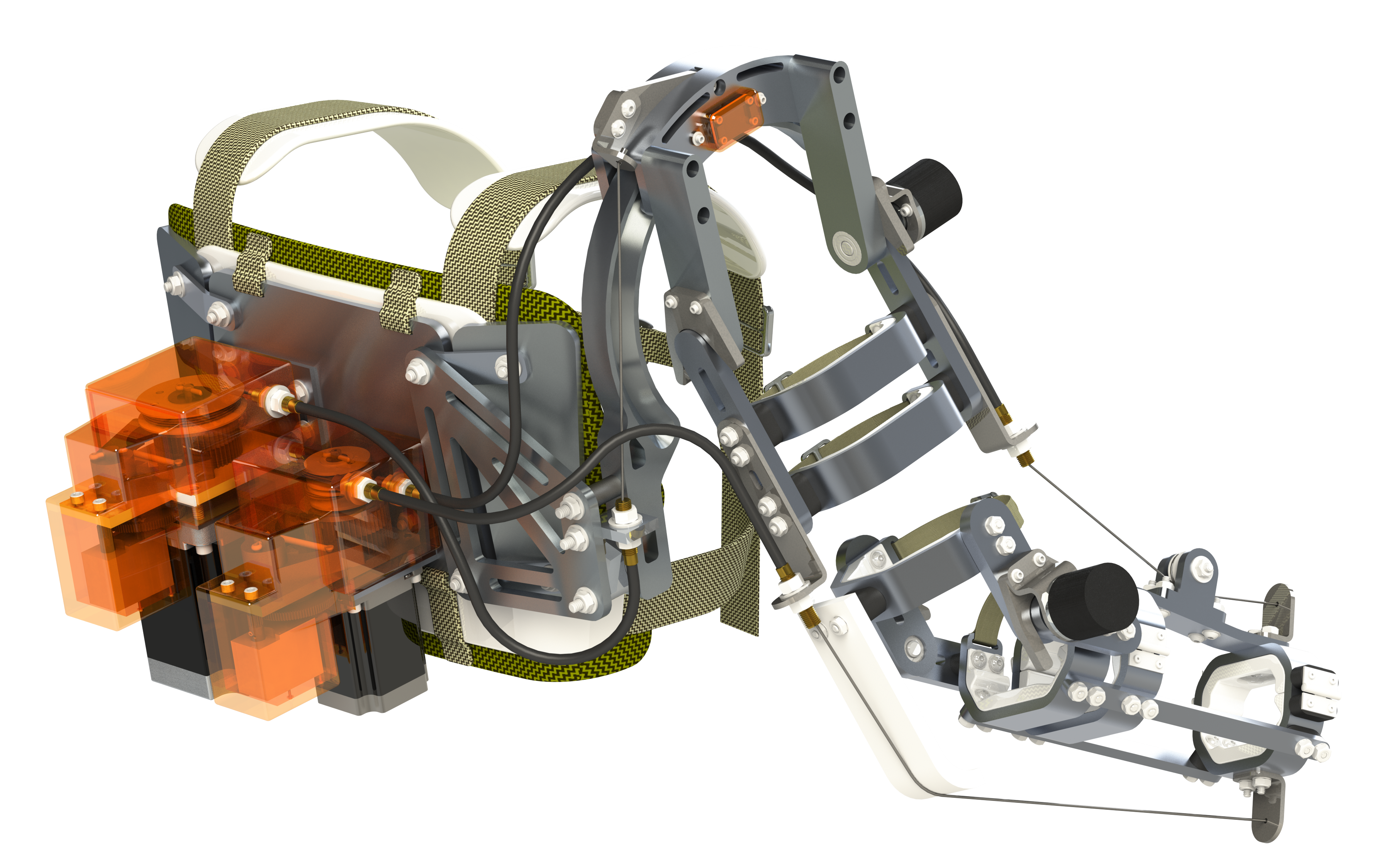
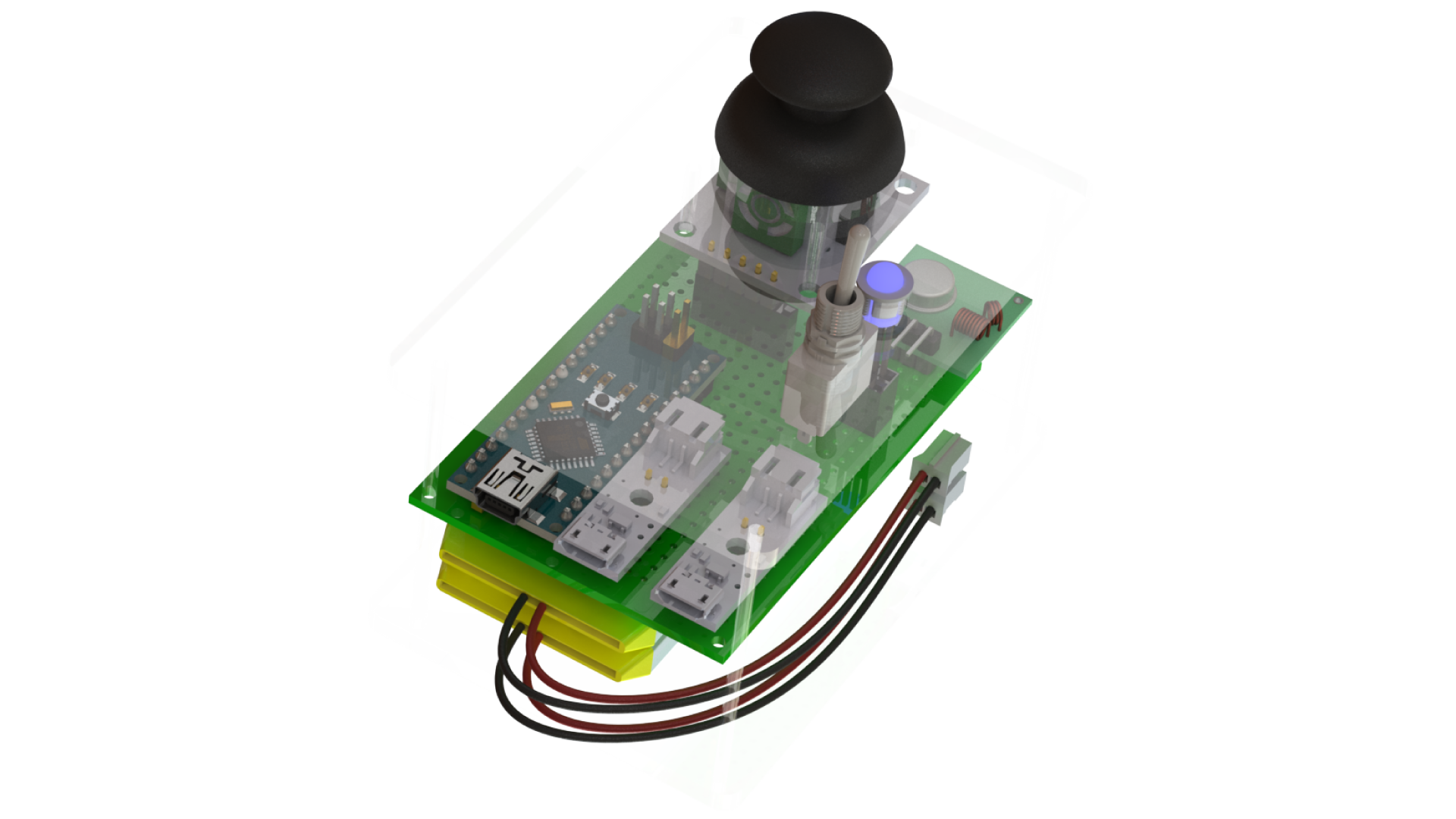
Skills Used:
- App Design: Unity 3D
- CAD: Solidworks
- UI/UX: Unity 3D
- Stream Processing: C++, C#
- Signal Filtering: C++
- Circuit Design: LTspice
- Circuit Fabrication: Arduino
- Website: https://sec2198.wixsite.com/powerarm
Preface
This was a submission to Columbia University's 7th annual Senior Design Expo; however, because of 2019 SARS-CoV-2 , projects were finished remotely and much of the hardware reamains in the prototype stage of design.
Executive Summary
The Power Arm is a cabel-actuated robotic exoskeleton arm design which uses bowden cables to transmit power from back-mounted high torque stepper motors that are regulated by a microcontroller and ratchet-pawl locking system. The device is remote controlled using input from a mobile GUI (or wireless remote), visulalizing in real-time the joint angles, power output, movement speed, and other parameters being calculated.
My Contributions
Desktop GUI
I made a GUI to run on the Rasberry Pi controlling the Power Arm. It's scripted with C# in Unity 3D. It's designed to visulalize in real-time:
- joint angles
- power output
- movement speed
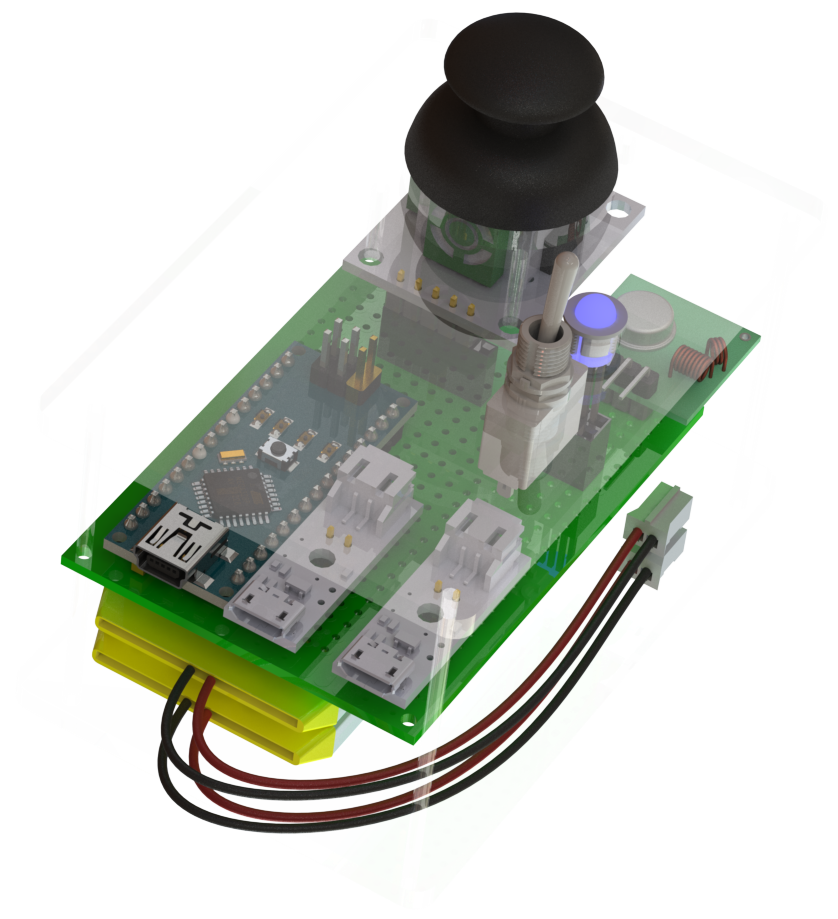
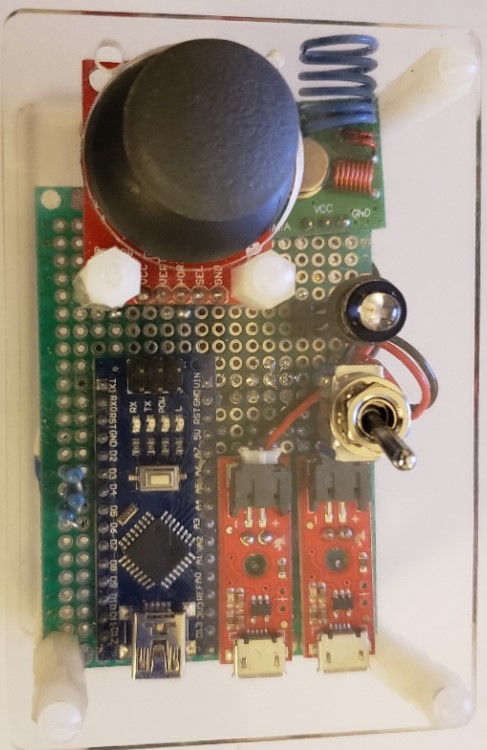
Analog Remote
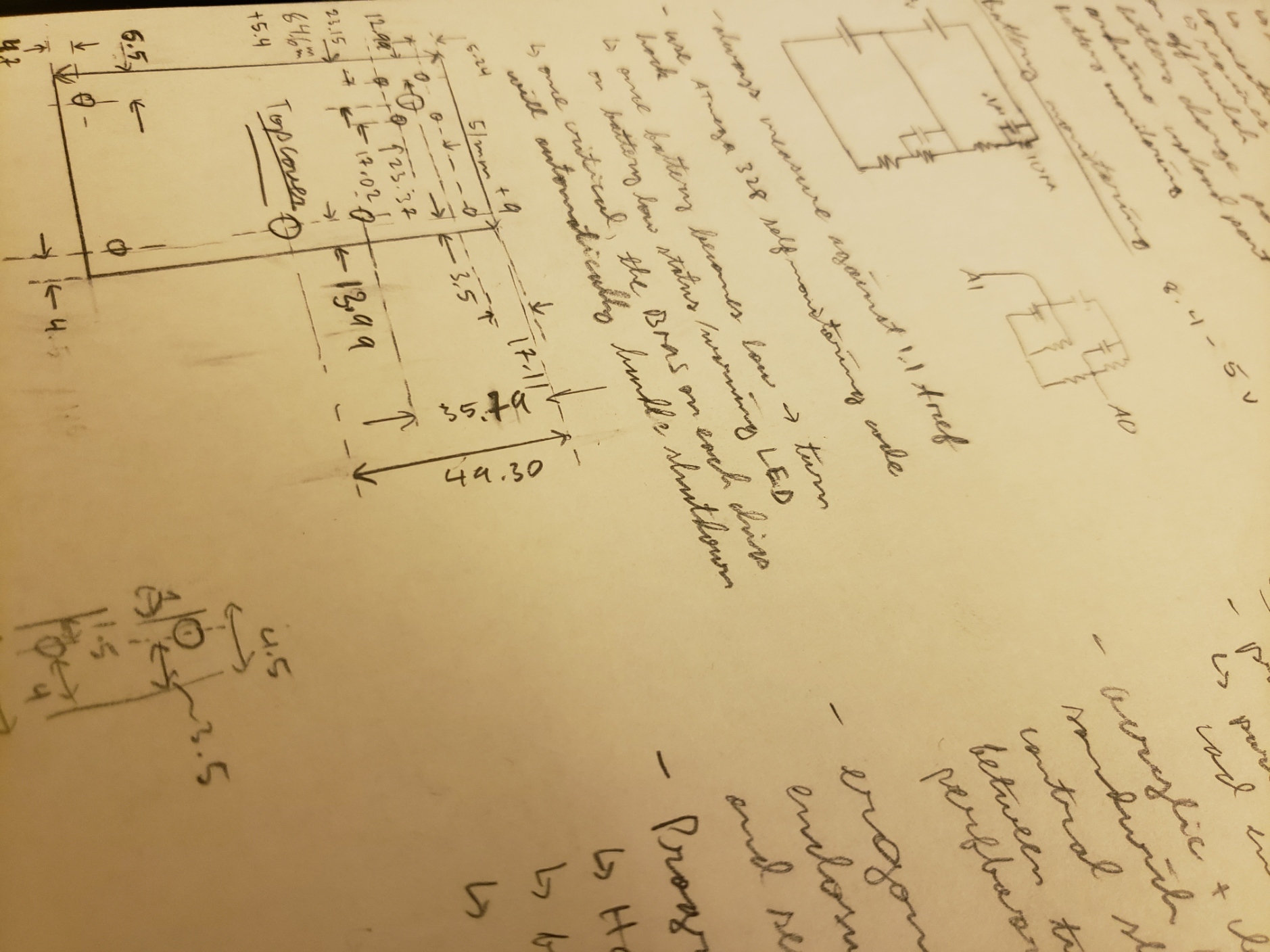
I designed and prototyped a wireless remote for single-handed operation. A touch sensor on the back acts as a
safty switch and an analog joystick acts as a throttle to move the end effector in a corresponding planar direction.
I made a mockup using Solidworks and wired the components to a protoboard.
Features:
- digital signal filtering
- wireless transmission
- status light
- battery monitoring
- rechargable via micro USB-B
Mobile Remote
I also adapted the GUI for mobile devices to increase accessibility. It features an interactive joystick and can replace the analog remote.Features:
- warning screen
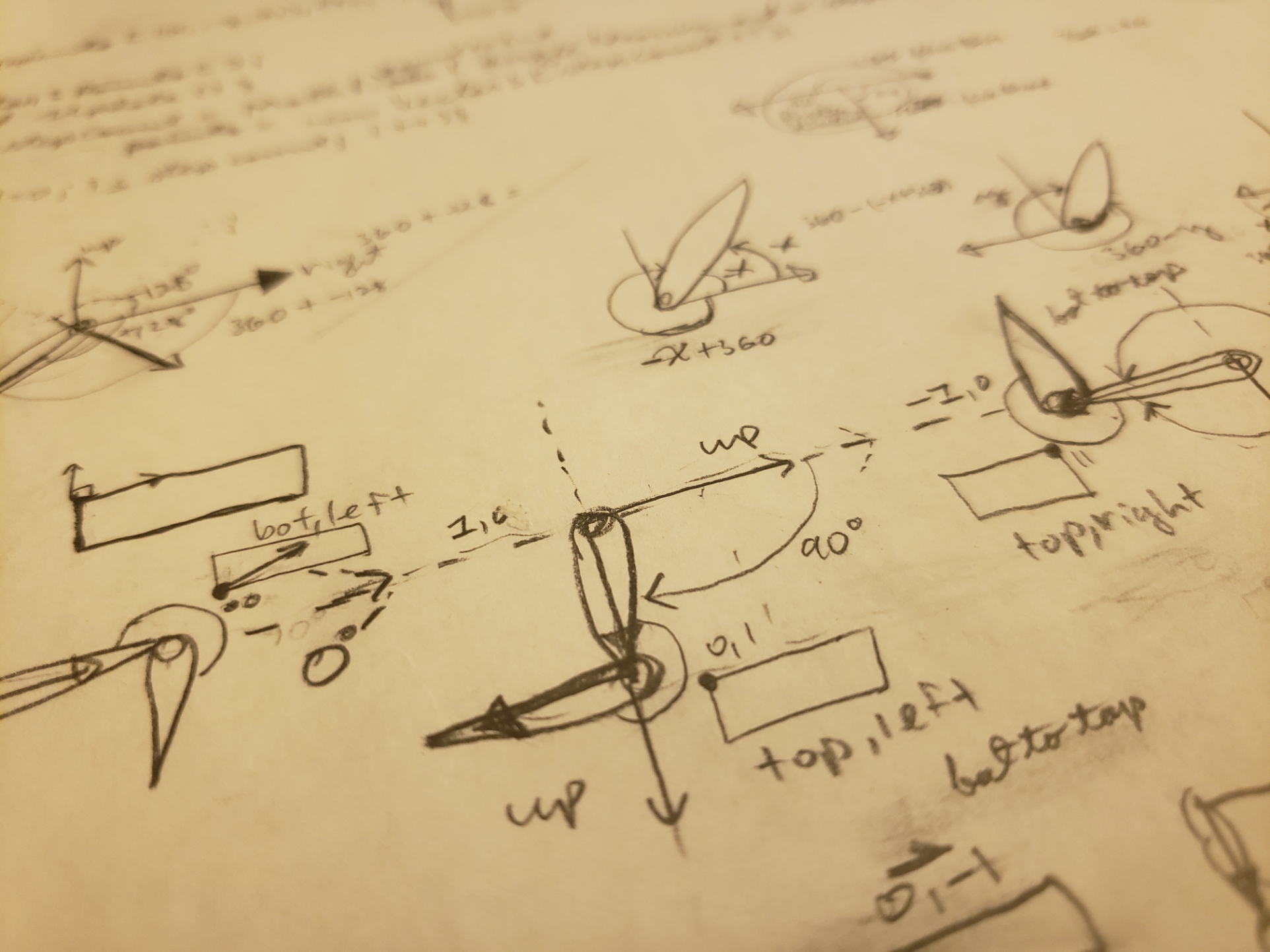
Demo Video
With my teammates and I as the co-stars and co-writters of this modest production, I was the video editor for our pitch video. I used Adobe Premiere Pro to immitate an old school infomercial - we wanted to give the project a little levity given the unforseen circumstances in which it ended.
Objective
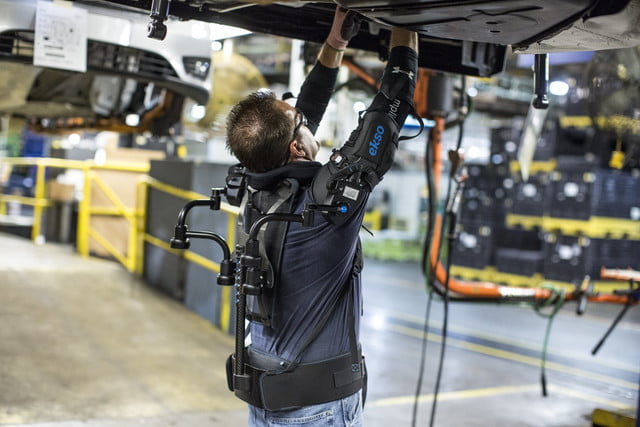
With a projected value of $5.2 billion by the year 2025, the market for wearable robotic exoskeletons is grow-ing at an unprecedented
pace. Competitors in this sector have been making waves with wearables that provide rehabilitative support or supplemental aid for a select worker demographic. Yet, jobs requiring
strenuous manual labor in every industry from automobile manufactures to courier and shipping services stand to benefit from more worker
friendly assistive tools because chronic back and joint pain can severely limit productivity and quality of life.
Thus, this project sought to aid individuals with limited strength/mobility and prevent long term fatigue for such workers
with a novel design that balances:
- Cost
- Portability
- Ergonomics
- Functionality
Parameters, Constraints, and Safety Considerations
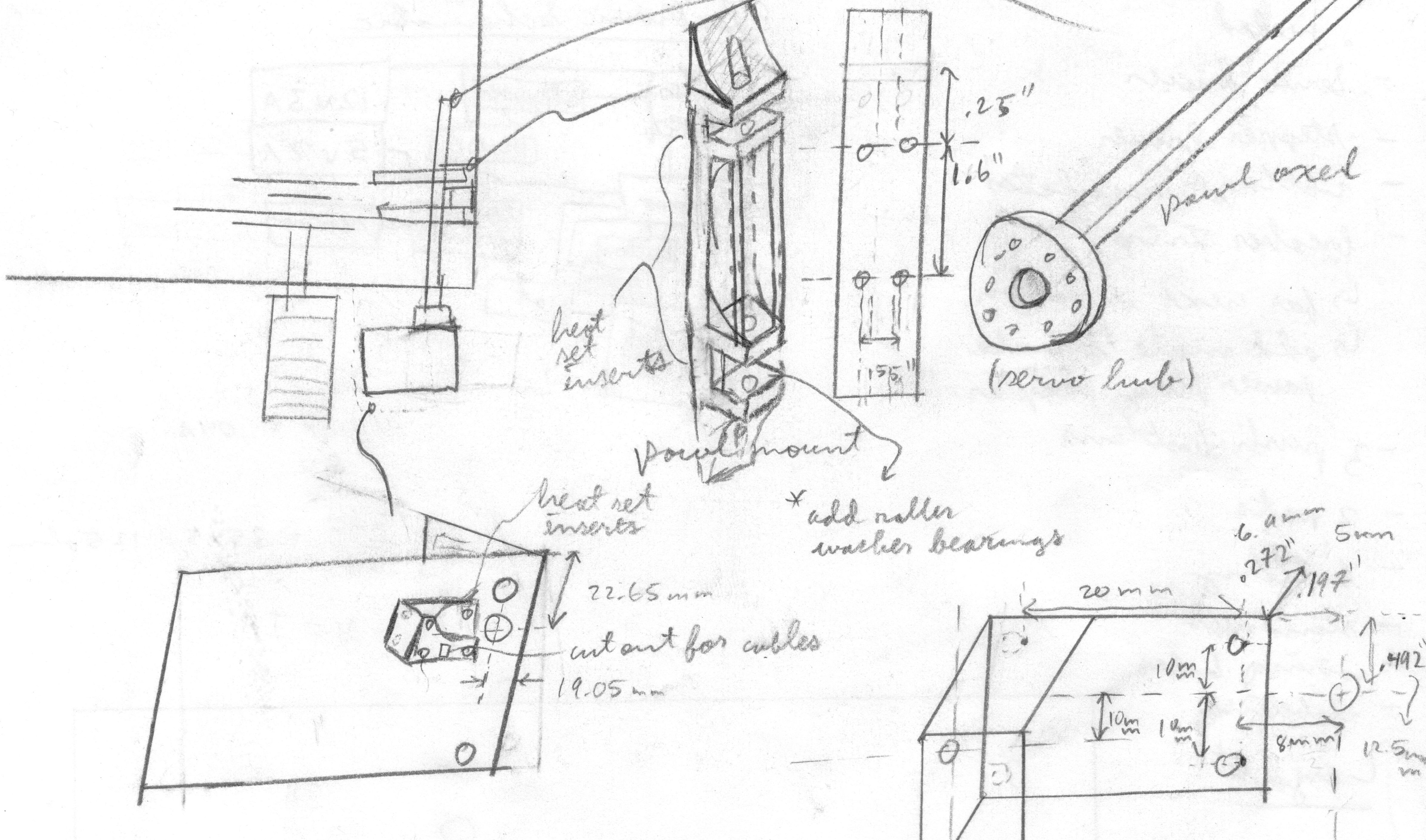
Whether it's for lifting heavy objects or getting assistive power when performing repeated tasks to minimize fatigue,
augmentative strength capabilities are useful for everyone. Such a device that can achieve such wide adoption will be
distinguished by its performance in three categories:
- Functionality:
- power output comparable to or excelling beyond what is currently available
- Availability:
- abiility to fit a wide variety of individuals and upper extremities of differing lengths and sizes
- Ergonomics:
- ease of use, comfortability, and portability that accomodates varied and extended uses
Our design is limited by the financial and time recourses available to our team, namely:
- Budget: $1000 + Sponsorships
- Time: Seven month deadline
Saftey Concern | Design Consideration |
---|---|
Over Extension or Sudden Actuation |
|
Unintentional Actuation and Sensor Noise |
|
Exposure to High-Voltage and Large Current | Applicable Codes and Standards:
|